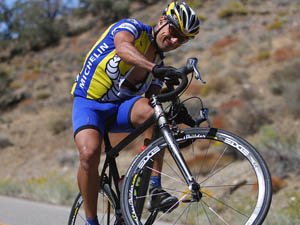
Years ago, as a budding young photographer, I cornered a very successful shooter and grilled him with many specific technical questions, and he surprised me by answering them all. Disarmed by his unusual candor, I asked him why he was willing to give up so many trade secrets. He answered, “I can tell you all the stuff in the world, but nothing I say to you is going to give you what I’ve got up here” (pointing to his head).
Rich Sawiris of Wheelbuilder.com reminds me of that photographer. He recently helped a teammate and me with parts and advice for a Powertap/carbon rim wheelbuild (my 2nd with Rich’s help), and his generosity was just as refreshing. Like that photographer, his openness betrayed a confidence in the breadth of his experience. His knowledge helped us deal with the challenge of building on a carbon rim, and thanks to him that wheel has remained true after a couple of months of heavy use under my big, powerful teammate.
I rang Rich up to learn more about wheels and wheelbuilding.
Andy Shen: When I first heard of Wheelbuilder.com, I pictured a single guy toiling away at a truing stand, but you’re a bigger operation that that, right?
Rich Sawiris: I don’t know if it’s what’s considered huge, but it’s not one guy any more. We have five wheel builders here, so we’re still pretty small, but we’re not a bike shop. The only thing we do is wheels, it’s kind of a different model, all focused towards wheels.
AS: I think you did some wheels for Kristin Armstrong?
RS: Yeah, we did some wheels she used…we originally got hooked up with her through Lipton and Craig Upton, and we worked with that team in ’07 and she became the US champion and the World TT champion the same year, so that was a really cool opportunity. At that time they had a Shimano sponsorship and Shimano didn’t have TT equipment, so that was great for us to get the nod.
AS: So when you see a pro wheel like hers, I think it was an 808 rim, what’s the difference between that wheel and a stock 808?
RS: Aesthetically it would just be small stuff. The set we built her had black straight pull CX-ray spokes, a similar spoke to what Zipp was using, but in black. Internally, at the time – actually they’re still pretty cutting edge – it had some really high end ceramic bearings. We reworked the internal spacing between the bearings so they rolled extremely smoothly. That was the big difference. Plus, for a light female athlete, especially a time trialist, where there’s not a lot of lateral load, especially standing and climbing load, we can go with lower spoke counts and still maintain excellent durability and gain just a little better aerodynamic edge.
AS: When you go with these ceramic bearings, do you have any idea what the power savings is?
RS: We’re working on some fixturing to actually test that. We work closely with a few cycling and automotive gurus as well as the folks at Ceramic Speed in Denmark. Those numbers are kind of elusive, you see the big manufacturers’ numbers and it’s hard to say whether it’s propaganda or not. But I think the data’s pretty clear that ceramic bearings are the real deal, it’s just that the differences are so small and difficult to measure that it’s just a tough thing to quantify without knowing how the bearings were installed and how much and which type of grease was used. I’ve seen advertised data that says 3 watts saved at 300 watts on a 6% grade, so 1%?! That seems a bit high.
AS: We talked before, and you said there was a big range in ceramic bearings, they’re not all created equal. Which ones do you like?
RS: I’ve used almost all of them. In general the Ceramic Speed stuff has been a dream to work with. I’ve never had a bad batch and I rarely see a bearing come back that’s failed in the field. I sent those to the Tour de France and sent them to Beijing under five Olympic teams. They never fail and they have very good technology behind them. Jacob over there is pretty good about setting standards as far as the precision of the races and the hardness of the races, as well as the hardness and they quality of the balls. They set the gold standard.
AS: Can you talk a bit about building a balanced and true wheel, as opposed to a cosmetically true wheel?
RS: You built a wheel there, and I think I gave you guys some good tips. You have a tension meter I assume. You can do two things. You can just build a wheel really true and send it out the door, or you can build a wheel and spend a significant amount of time measuring 100% of the tension, balance it, re-balance it, and go through and make sure it’s cosmetically true. That process doesn’t lend itself to mass production. Some places really have to pump the wheels out, so producing them at a high volume level with balanced tension is just too time consuming.
If you look at a cross section of factory built wheels from a few manufacturers, it’s interesting to see the different signature builds of each wheel builder. Some build with extremely high tension, often over-tension, while others produce wheels that are cosmetically straight but have wildly varying tension uniformity.
If you don’t have a well designed production standard – where 100% of your product is measured and built consistently – it creates a lot of variance. Obviously, the process takes significantly more time to implement.
AS: All things being equal, would you build a wheel with as much tension as a wheel can take? Does that make the wheel better?
RS: More tension doesn’t make a wheel better per se. You don’t want to tension it to the point where any more and the rim would break, because you have the other components to consider. It’s not typically the rim that’s breaking, or giving you stiffness issues, as much as it’s the hub or the axle or the spoke configuration. So no, you wouldn’t just run it up as high as possible. The most obvious case is a front wheel. If you’re radially lacing, you can put a lot of stress on flanges, and running the tension up to 120 kg on a front wheel – even though the rim can handle it – can put too much stress on the hub flanges.
On rear wheels, you do want tension really high, especially if you run Campagnolo configurations, because you have such a large imbalance between non drive and drive tension, sometimes as much as 70% on the drive side, 30% on the non-drive side depending on the hub configuration. Loose spokes will frequently be the ones that fail, not tight spokes, so typically it’ll force you to run the drive side tension up a little higher than you would, or at least to their maximum, so you can have sufficient tension on the non-drive side.
AS: Would a tighter wheel actually feel snappier? Would you actually be able to feel that laterally?
RS: No, that’s a big myth. It would be nice to say, “We build a better wheel ’cause it’s tighter and laterally stiffer,” but the data doesn’t show it. If you have a soggy wheel, where everything’s at 20kg or 30kg, it’s going to feel pretty poor. But if it’s in the ballpark, it feels pretty good by hand, and it’s straight, typically the rest of the stiffness characteristics are just inherent to all the components that you’re using. So if you just took a factory built wheel that’s slightly on the loose side, it wouldn’t feel too different from one that’s at maximum tension.
Really the difference between those two wheels isn’t how stiff they are, as much as the huge difference in long term durability. The higher, more uniformly tensioned wheel is the one that’s going to last forever, within reason. It’s the one that’s not going to break spokes, it’s the one that’s going to stay true. Somewhere down the line the loose one, as things soften up, will likely get to the point where it feels a little soggy.
It’s always difficult to quantify, when people ask, “What difference will I feel in your wheels vs. a factory built set?” There is a nice difference in how smooth a well built set of wheels feels when cornering, climbing, and descending, but the real value Wheelbuilder brings is in reliability and long term durability. We also do a better job of matching athletes with the most appropriate components for their riding style, weight, and race requirements based on a lot of internal testing.
AS: You make a very big deal about even spoke tension, and I think you catalogue every spoke of every wheel.
RS: Yeah, we have digital meters and output, it gets a little bit over the top to actually keep a record of every single wheel, as far as keeping it on file, but every single one you can be sure goes through that measurement process, and you can be sure it gets done five times before the wheel’s done. It’s a good thing you guys had an opportunity to play around with a carbon wheel build. You can see a five minute truing job will get you close, but it takes a lot more to get the tensions right. We use a build process that considers the structure of the wheel under load rather than viewing what’s obvious in a truing stand.

AS: In terms of longevity, where’s the mechanism wherein even spoke tension promotes longevity? Is it because you’re not going to have a stray loose spoke that’s going to flex more?
RS: Typically you’re not up against the strength limitation of any of the components of the wheel. The real problem is fatigue, and since fatigue is your biggest enemy, a loose spoke will almost always fail first. I’ve seen some data showing a 70% reduction in fatigue life if the spoke is loose enough. So if you have a perfectly true wheel, but one spoke is loose and the two next to it happen to be tighter (so it cosmetically looks straight), it’s not distributing load evenly. What will happen is that loose spoke will ultimately break with what little load it’s carrying, and it’ll overload the one that’s next to it. You’ll have all kinds of trouble with unpredictable fatigue characteristics, because while every spoke is seeing a million revolutions, they’re not subjected to the same load for a million revolutions.
AS: It’s almost backwards, where the spoke that doesn’t have a lot of tension actually sees more stress. Is that just because the tension’s low, it’s going to flex more, it’s going to be more vulnerable at the head?
RS: It’s not that it’s seeing more stress as much as it’s seeing a different kind of stress. If it’s properly loaded, you might see a spoke go from 120kg down to, let’s just say 80kg, and then back up. It really goes tension-tension – it never goes slack. If the spoke’s initially only at 30kg, every revolution of the wheel will cause it to go from tension into compression. You can view a spoke as a string, it can’t really go into compression, it just gets loose, goes slack, and then gets tension again. It’s kind of a jackhammer effect, an impact load happening at the head and the neck of the spoke, which it’s totally not designed for. Spokes are designed to be totally under tension, slightly less tension and slightly more tension, but not to go to no tension and then suddenly be impacted at the neck.
AS: You’re helping to design Powertaps…
RS: Yeah, designed the mountain version of the PowerTap. We designed it here and got fifteen prototypes manufactured. Saris has a good relationship with Trek so they were able to torture test it.
I just finished the fixed gear version of the PowerTap, and it looks really cool. The market for track PowerTaps is pretty small relative to road units, so we were able to get ownership of the fixed Powertap from Saris. The track community is really excited about the hub, so globally the numbers make sense for Wheelbuilder.
AS: So you’re going to be selling the track PowerTap?
RS: Yeah, I have 200 of them finished and they’re here, just waiting for final approval from Saris to start allowing them to be sold in the marketplace.
AS: With disc brakes and fixed gears, is it the same issues with reverse torque?
RS: The way we got around the problem of reverse torque on the disc brake version was by de-coupling the braking loads from the torque tube. So if you look carefully all of the brakes are mounted to the hub shell rather than the torque tube. The hub shell has the ears for the disc rotor machined in. The brake does not touch the torque tube at all. Otherwise you’d have issues with reverse torque coming in from one side, positive torque coming in from the other side. If you brake really hard, you could possibly unthread the torque tube out of the hub shell. It can’t be a similar solution for the track, right?
No, for the track it’s different. It’s very difficult to create that much negative torque to be able to break the hub shell loose. In contrast, it’s very easy to generate that much torque with a disc brake. You have the condition where you could be airborne with a heavier rider, and the brake is completely locked in the air, so when you land, you have a huge amount of torque that comes in from a locked brake. It’s pretty difficult for a human to generate that amount of torque, which can be greater than 150 ft-lbs of torque. That’s some serious impact, it’s what a small 4 cylinder car engine would generate.
AS: Recently I broke out an old set of 32 spoke 14-15 gauge, Mavic Reflex wheels. I was surprised at how crappy those wheels felt, they just made the bike feel worse, kinda made me not want to ride the bike. When you spec wheels, do you make any concessions towards feel, or is it strictly about performance?
RS: Feel is, I don’t know what %, but it’s definitely more than 50% – that’s definitely what we talk to people most about. Whether it’s “I have back problems,” or “I ride double centuries,” or “I really don’t care about ride comfort, all I really care about is ultimate stiffness,” and there are wheels all over the map to address each issue. So balancing stiffness characteristics with respect to how it corners, versus vertical compliance, are definitely in the DNA of each type of cross section of rim and something that we really try hard to take into account.
I used to be an automotive engineer. I worked as a test engineer for Toyota’s research and development. The sports cars were actually an easier engineering job as far as setting targets, because they’re purpose built. People are always willing to accept that driving a Corvette is going to be noisy and rough and it’s probably going to hurt your back, but it’s going to be very fast and handle well. The most difficult vehicles to design were cars like the Camry, where it’s an appliance. You wanted it to do absolutely everything. You didn’t expect it to handle like a Corvette, but other than that it had to do everything well. Looking at wheels, people want a wheel to ride really well, handle really well, corner really well, brake in the wet, be lightweight, and you want it to have excellent durability. There aren’t many wheels that can do all of that.
So if you say you don’t care if it jars your back, this is just a crit wheel, and you weren’t going to race it in the wet, then you’d ride around on a very stiff deep section carbon rim. It feels awesome under race conditions , but if you go over any cobbles it rattles your teeth.
AS: So what are the parameters you’re playing around with? Rim choice, spoke count, spoke gauge?
RS: Spoke counts make pretty small differences. Spoke counts primarily balance your aerodynamics as well as your long term durability. If you put a 200 lb rider on a 20 or 24 spoke wheel, then take the same rider on a 32 spoke version of the exact same rim, in general it’s not going to feel too much different. It will have some subtle differences in ride comfort and stiffness, but you’ll see more dramatic differences in fatigue life. So spoke count is not a huge variable in changing how a wheel feels, however, some wheels can handle low spoke counts and some can’t. For example, if you look at a Mavic Open Pro, or similar traditional box section rim – if you were to try to make them with 24 spokes, it would be a disaster for heavier riders
A rim cross section performs similar to an I-beam on a building. As that I-beam gets taller between the flanges it gets incredible stiffness in bending. It’s exactly the same with deep section wheels. A wheel like that Open Pro or a Reflex, if you were to take all the spokes out, you could almost twist it like a pretzel by hand. You can apply a little bit of weight to it and you can see it’s extremely flexy; the cross section doesn’t have a lot of strength. But if you tried that with a Zipp 808 for example, you wouldn’t be able to get it to budge at all. As those cross sections get deeper, they get stiffer. As they get stiffer, you can reduce spoke counts because there’s no localized deformation in the rim. So spoke count is not something you can choose in a vacuum, it goes hand in hand with what kind of rim you’re spec’ing.
AS: When I first started building wheels, I took apart a set of 32 hole 14/15 gauge spoke wheels and rebuilt it with Revolutions (thinner 14/17 gauge spokes). And I could’ve sworn those wheels felt much better, but of course I couldn’t go back and ride them with the original spokes to compare. Was I imagining that or was that for real?
RS: No, selecting spoke count and selecting spoke type are two very different things. It’s pretty subtle but it can be felt, especially if the rim is already not very stiff. The super thin spokes have pretty poor lateral flexibility, as you can imagine, there’s not much cross section there. If you look at the difference between a Revolution and a DT Champion (straight gauge 2 millimeter) in the exact same wheel build, you have a pretty significant difference in lateral stiffness of the spoking system. They just can’t support as high a lateral load. It plays less of a role as the spokes go into deeper section wheels, which are significantly stiffer, and the spokes get significantly shorter. So if you were to put them in a Zipp 808, it’s not as great a difference as those wheels get stiffer and deeper.
There are a lot of people who’ll tell you how different their wheel builds will make the wheels feel, yes, if you did a good job and everything was tight and uniform, it’s going to feel better. If you have a lot of spokes as well, that evenly distributed load does make that structure feel like it’s solid.
AS: Everyone loves CX-Rays. Are they really that much better, and what makes them better?
RS: The great thing about CX-Rays, is fatigue resistance. Sapim claims their fatigue life numbers are three times that of their other spokes like Sapim Race or Laser. The number one enemy of your wheel is fatigue of the spokes. If nothing else happens like a crash, ultimately your spokes will start to break. If they can extend fatigue life by three times, it makes it extremely appealing to anybody who’s building a wheel, especially a builder like me who wants his wheels to last a long time.
In addition, they look sexy ’cause they’re bladed, and they’re about 27% lighter than what you’d get out of a 14/15 double butted spoke. You can almost put them up against a Revolution or a Laser, so you get the weight advantage of the really light double butted spoke, you get the sexy look of a bladed spoke, you get better fatigue life, and they’re the only bladed spoke you can get in super short lengths. We use them for pro BMX guys, and we get them down to 186 mm, so we can also use them in Zipp 1080’s. They’re pretty hot.
AS: And of course, being bladed, there’s no windup.
RS: From the production side, bladed is always a dream. You don’t have to pinch the spoke and have a really good subjective feel for how much windup you’re doing in the forward direction, then the reverse direction, then have to manually unwind each one. You can just hold it in place, and when it’s done it’s done.
AS: How do you feel about carbon clinchers?
RS: I’m a big fan of them, but I think people try to make them a do-all when they’re not a do-all wheel. For example, none of the carbon clinchers have very good braking performance in the wet. That’s a minor thing because most of us don’t like to ride in the rain, and in a lot of cases, they’re your really nice wheels, and you just don’t want to ride them in the rain.
The other limitation of every carbon clincher made by any company, Reynolds, Edge, Campagnolo, the Gigantex stuff etc., is that all of those wheels have heat sensitivity issues. And it’s not a flaw. If you put the wheel in the oven and cure it at 300-350 degrees, that means you don’t want to see braking temperatures that exceed 300-350 degrees in the real world, or what’ll happen is the rim will turn back into a buttery jello, and the tire pressure of the clincher will just fillet the brake tracks open. It’s a very common failure mode. In general, if you’re pretty lightweight you won’t have a problem. We sometimes run into problems because the wheel is so strong people think they can do anything with it. If you put a 200+ lb rider on it and he’s a nervous descender on a steep grade, you’re in for trouble. A large percentage of the failures I’ve seen happen in those situations. It doesn’t mean you can’t brake extremely hard, it just means you can’t do it for prolonged periods of time with no cooling on the brakes.
Those are the two downsides of the wheels. The upsides are they’re incredibly durable, even for impact. It’s amazing how much impact they can sustain.. Of course, if you impact hard enough, the failure mode is going to be a crack rather than a bend, but in general they build into very, strong wheels from all manufacturers. And you’re looking at a 150 gram savings on the rim by going all carbon. As well as stiffness – the carbon clinchers are among the stiffest out there.
AS: Is it all carbon rims for you? Do you ever build on metal rims?
RS: We do build aluminum, but carbon is really our specialty because it takes a certain expertise and a lot of practice and specialty equipment to get it right. It helps to have confidence from the cycling community to rely on us as the source for precision carbon builds. That credibility allows us to put 350 carbon rims on the rack, so we’re able to build any combination. Until you get to that point, it’s kind of a pain because inevitably the rim you need to build isn’t in inventory.
We build quite a bit of aluminum because one of our biggest products is PowerTap. Not only do they go into carbon race wheels, but people want them in training wheels and aluminum is a excellent choice because of cost and durability. For triathletes, we make disk covers, which make a lot of sense if you’re on a budget. A great setup is to run a Flashpoint 80 front wheel, so you get a pretty good bang for your buck on that, and for the rear you run your PowerTap aluminum training wheel and the disk cover. You’re basically on what won the TT Olympic Gold for Tyler Hamilton. The time saving would be very similar to a Zipp 900 disk with an 808 front wheel.
AS: Why’d you leave the automotive industry?
RS: I wanted to do something I was really passionate about and I have a lot of pride in what I do. I enjoyed automotive, I was into cars, still am I guess, just not as much. It was something I wanted to do on my own, and I wasn’t happy in a corporate structure being indoors all the time.
AS: So you were a bike racer, worked in the auto industry, and decided to get into wheels?
RS: Wheels were something I’d done forever. At my very first job I worked for a motorcycle wheel building place called Buchanan’s. It was when Supercross was coming on the scene in the 80’s, I built Harley Davidson and Supercross wheels, even spoked automotive wheels for old Jaguars and some of those cars. I raced BMX at the time, built my own wheels, built the motorcycle stuff and just never really dropped it. Then I got a mechanical engineering degree, geeked out a little more on it because I could measure and quantify what I’d previously done by feel. I developed a process on how we make our own tensiometers. One thing just led to another, I mainly wanted to run my own business and do something I could be really proud of and be the best at. Wheels were the first choice on that.
AS: I saw one of those motorcycle building TV shows, and someone built a motorcycle wheel. It had a million spokes and they were incredibly short and thick. It was the same thing as a bicycle wheel but it couldn’t be more different.
RS: Yeah. And when you tune them you can’t flex them locally like you can with a tensiometer, you can bang on them with your wrench acoustically and hear the differences. Easton does a really cool thing, they build a lot of the same exact wheel, so they have an acoustic signature where they just ping the spokes. Your ears are really good as far as telling the difference between spokes, even better than a tensiometer. The only problem is you don’t have an absolute number.
AS: Those first wheels I built I went by a pitch I got from a Sheldon Brown article.
RS: I was an acoustic engineer before, and that’s what I did, a lot of sound testing. If we were doing tire development, and we went out at 8 AM and if we had six tires to test back to back, you couldn’t go to lunch because you don’t hear the same way with a full stomach as you do on an empty stomach. You literally have to listen back to back, but when you do, it’s amazing the subtle differences you can hear. If you have a 5 kg difference between two spokes, that’s not really a big difference on a tensiometer, but by plucking standards, it’s very easy to hear with your ears.
“my big, powerful teammate”
BRUBAKER!?
Yes, big strong boy.
As a cat. 4 squid buying a relatively low-end aluminum PowerTap wheel, I was pleasantly surprised that Rich had all the time in the world for me on the phone, spec’ing the rim, spokes, rim tape – everything. Happy to discuss all the options. No hard sell. Pretty cool. Fast forward to today, and, yes, I’m still a cat. 4 squid. But that’s not Rich’s fault. Dammit all. –Greg D.
i’m sopriced that powartap dint get you to cat 1 lol
And I’m surprised you’re able to get through the day with such awful spelling.
How busy can a wheel builder possibly be?
To 4:15,
I am sure that the post timstamped at 9:40 was a deliberate reference to an entry which was subject of prior ridicule, perhaps a few weeks back.
It is the sometimes vague subreference that gives this site a true “insider” feel to the original fan base, now that we seem to have generated some critical acclaim outside of our little corner of the universe.
Due to this certain items enter the common vernacular, such as the term “idot”. To the unwashed, it it poor spelling and/or grammar. Just don’t expose yourself as an outsider by asking “Who’s Evie” or by comparing finish time for Cat 4’s against any other field in an attempt to see which was the harder race – forreals!
wholly poo, yo.
cat 4s are awesome!
Next on Bravo: Lonely Cat 4 Guy with an Evie Eye
“You’re basically on what won the TT Olympic Gold for Tyler Hamilton.”
Tasty combo: Zipp 808’s and 100 IU of EPO.
ทางเข้า sbobet
It’s really a nice and useful piece off information. I’m glad that you simpply shared
this helpful information with us. Please keep us up to date like
this. Thanks for sharing.
And I’m sopriced that you didn’t get the joke douche.
Anyone who is interested in spoked bikcycle wheels should read THE book on the subject, “The Bicycle Wheel” by Jobst Brandt. It discusses how a wheel works and how to build good solid wheels.